By GSCB Staff
This is the first in a series of three articles using information from the USDA General Technical Report FPL–GTR–169, looking at specific characteristics of degree of movement, sealant-substrate compatibility and adhesion-surface preparation and how these apply to portable buildings.
In traditional portable sheds, weather tightness is not usually as critical as in a home or other residential building. With “sheds” becoming larger in size and filling roles previously reserved for traditional buildings, the ability of sealed windows and doors to withstand the rigors of moving presents a challenge. But this is a feature necessary for the “sheds” to compete with traditional building techniques and affects the life span of the building.
In discussions with window and door manufacturers, the typical first recommendation on sealing is to make certain the opening is square. This minimizes irregular features and simplifies sealing whether using sealant or tape product. Other aspects that must be considered when sealing doors and windows in traditional buildings are porous vs. non-porous substrates and condition (clean, moisture free, etc.) of the surface.
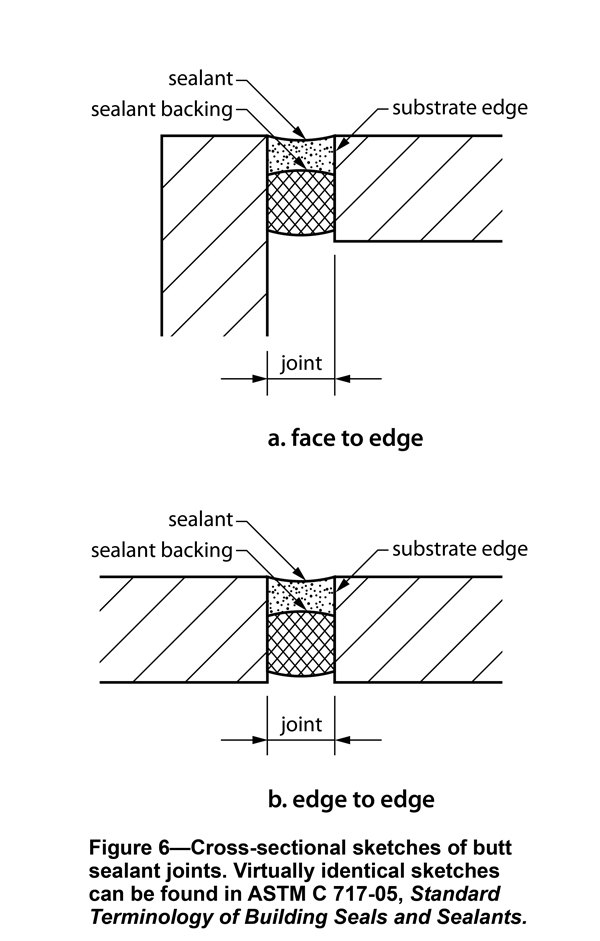
These same factors still apply to portable buildings, but face additional challenges. Portable buildings lack the rigidity of permanent structures, which increases the importance of adhesion and flexibility when sealing doors and windows. These challenges are most notable in climates with extreme heat, cold or sun.
From the USDA General Technical Report FPL–GTR–169:
“Standard C 920 specifies resistance to cracking at elevated temperature, at cold temperature, and after exposure to ultraviolet radiation. Conformance with ASTM C 920 generally is an indication of superior performance, although a simple statement of conformance to the standard does not fully describe performance. The standard recognizes five different classes, categorized by the degree of movement between substrates that the sealant can tolerate. Classes range from a Class 100/50, indicating that adhesion and cohesion meet acceptance criteria at 100% elongation and at 50% compression, to a Class 12½, indicating that adhesion and cohesion meet acceptance criteria at 12.5% elongation and 12.5% compression. ASTM C 920 (indirectly) specifies limits on maximum allowable shrinkage of sealant during extended cure. Latex acrylic caulks usually shrink enough during extended cure that they will not meet this particular requirement for conformance with C 920. Uncured latex acrylic sealant can, however, generally be applied successfully to cured sealant of the same type. A wide variety of emulsified resin (“latex”) caulk is available, ranging from low-cost products that may incorporate vinyl rather than acrylic polymers and that meet none of the performance requirements of C 920 to products that meet all except the shrinkage limitations of C 920 Class 25. Latex acrylic products are in many ways the easiest of the sealants to use. In residential building, where the knowledge and skill of applicators may not be well developed, latex acrylic sealants may provide performance as effectively as silicone or polyurethane sealants even though they do not match the performance of these (usually higher cost) sealants in controlled laboratory testing.
Joint Dimensions Matter In narrow joints, a given amount of differential movement between substrates translates into relatively large strain rates in the sealant. ASTM C 1193 makes no recognition of sealant joints narrower than 6 mm (0.25 in.). Figure 8 shows a 6-mm- (0.25-in.-) wide perimeter butt sealant joint around a residential window, which was in accord with the window manufacturer’s installation instructions. ASTM C 1193 states that acceptable sealant joint depth varies with joint width and sealant type. A generic rule for joints up to 13 mm (0.5 in.) wide is that joint depth should not exceed joint width. Minimum acceptable joint depth varies with the sealant type, and sealant manufacturers rarely if ever provide minimum depth recommendations to retail customers. With butt joints (Fig. 6), some minimum depth dimension at the substrate surfaces is necessary for adequate adhesion. The hourglass shape of the sealant cross section that can be seen in Figure 6 is considered desirable, as it provides the greatest possible adhesive-bond area at substrate surfaces and provides a region of relatively low stiffness at mid-width of the joint. Tooling of sealant results in surface concavity that provides in part for the hourglass shape of the sealant cross section. With sealants that shrink during cure, concavity of the cured sealant joint surface is likely to be accentuated, and as a result, sealant depth at joint mid-width may be less than anticipated. When using sealants that shrink, making some trial joints to identify cured sealant depth at joint midwidth can be instructive.”
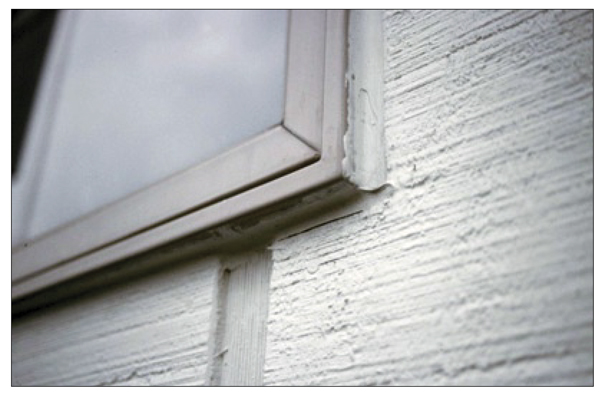
Figure (Pic.) 8—A perimeter sealant joint around a contemporary flanged window. The joint is of appropriate width at 6 mm (0.25 in.). The joint had been in service for roughly 3 years when photo was taken. Joint is mostly intact, but some adhesion failure is evident at lower right corner. As is common in residential construction, neither bondbreaker tape nor sealant backer was used. Joint failure is likely the result of three-sided adhesion, an unprimed siding edge, and other-than-ideal sealant width–depth ratio
(sealant depth exceeding width).
Takeaways from the technical bulletin:
• The gap between different substrates has an obvious effect on the ability of the sealant to seal.
• Tooling the sealant (using a finger, plastic spoon, etc.) to create a concave surface increases the flexibility of the sealant.
• ASTM C920 evaluates how much stretch different sealant types tolerate; this affects shrinkage over time and flexibility/motion that can occur when moving.
The best weather-tightness will occur when the openings are square and sized as precisely as possible for the window and door. Select the best sealant for the environment and substrates it adheres to and complete the joint with tooling to increase the flexibility of the seal to withstand shrinkage and the additional rigors of moving the building. GSCB
Useful links:
ASTM C920: https://www.astm.org/c0920-18.html
USDA General Technical Report FPL–GTR–169: https://www.fpl.fs.fed.us/documnts/fplgtr/fpl_gtr169.pdf
Please read the next article in our Product Series for more.