By GSCB Staff
Last year had plenty of challenges. Lumber prices are erratic and still higher than historical norms, manufacturers and builders have had to deal with material shortages, and everyone is dealing with longer lead times getting raw materials or supplying their customers. But there have also been opportunities. Let’s look at a few of the challenges and opportunities of 2021, and what might be coming our way throughout 2022.
Material Challenges
You’d be hard-pressed to find some sector of construction that didn’t have at least some supply disruption in 2021. We’ll focus on steel and lumber, the two most common materials used in — and critical for — all types of low-rise construction and special-use buildings.
Early in the pandemic, steel companies shut down production and inventories were depleted, creating a raw material shortage. Overseas and domestic shipping problems (and other reasons) challenged the supply and resulted in higher prices in 2021. However, demand remained strong. At the Steel Summit meeting in August 2021, hosted by Steel Market Update, industry experts predicted a strong 2022, with some recessionary activity potentially in the second half of 2023.
Lumber mills were also shut down and builders (and do-it-yourselfers who had time on their hands) quickly cut through the lumber supply. The result was a decrease in supply, and an increase in demand. The inability of domestic mills to rapidly increase lumber production to meet the demand resulted in an unprecedented increase in lumber costs. The Random Lengths Framing Lumber Composite Price, an industry benchmark, increased about 175% between April and September. In May 2021, the FLCP topped $1,500 per thousand board feet ($1,500/mbf). A report from the National Association of Home Builders (NAHB) said, “The production gap, and the material cost impact, can only be closed via a significant increase in domestic production, more U.S. imports of lumber, or a significant substitution to other building materials.”
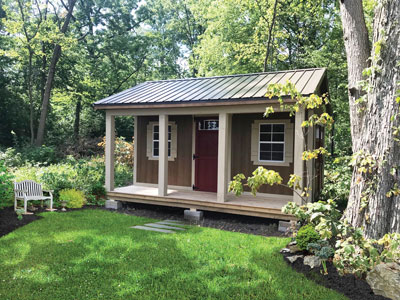
To understand current lumber market activity, listen to the Structural Building Component Manufacturers’ (SBCA) bi-weekly Lumber Connection podcast (https://www.sbcacomponents.com/media/lumber-connection), on which lumber market professionals “discuss today’s market and explore tomorrow’s trends.” In the January 17 podcast, Ken Timmins and Justin Binning, both with American International Forest Products (AIFP, lumber.com), discussed the lumber market imbalance. During this particular podcast, they explain why the lumber market is under-inventoried due to transportation issues, the weather, and COVID-19. In part, the mild weather in the fall and early winter kept construction going strong. Jobbers worked through their inventory at the end of 2021 and the work kept coming in; demand continued to outpace lumber production. Plus, the late-year holidays and COVID outbreaks in sawmills caused mills to shut down for weeks at a time. Wood continues to leave plants and lumberyards, but logistical issues and COVID continue to have a serious impact on the volume entering the market.
They said there’s no quick or perfect fix for the supply chain issues, and you have to roll with the weather when it comes to getting your jobs done. They recommend keeping close touch with lumber suppliers and stay up to date on the lumber price and availability information so you can make informed decisions when it comes to running your business.
Many suppliers, not just lumber suppliers, have pointed out there’s not a single break in the supply chain; there are many. Some of which are:
- Ships loaded with filled shipping containers are awaiting off-loading off the California coast.
- Rail car and truck shortages.
- Shipping yards are full, so there’s no place to hold more containers before they continue to their destination.
- Container shortages due to filled containers being tied up in the intermodal transport snafu. (Container shortages will also have an impact on those companies that specialize in converting shipping containers into ADUs and other modular buildings.)
Expansion Plans
Several North American steel companies are in the process of adding production. While some of these projects are not directly aimed at steel for the construction market, any new capacity will help to ease overall supply constraints.
Blue Scope has new capacity expected to come on stream in Q2 at its North Star steel mill in Ohio.
Big River Steel, now part of United States Steel Corporation (US Steel) has a major expansion underway in Arkansas, which should be finished mid-year 2022.
US Steel has also committed to a new a mini-mill at a site yet to be announced, with construction to begin in the first half of 2022 and production expected to begin in 2024.
Steel Dynamics has announced plans to expand at its Terre Haute, Indiana facility as well at its Pittsburgh Techs Division. Some production at its new Stinton, Texas EAF operation went online in 2021, but weather delays has put behind the opening of the primary facility, now expected to come on stream in the second quarter of 2022.
Nucor has plans for a new steel sheet plant in either Ohio, Pennsylvania, or West Virginia.
Ternium and Arcelor Mittal are committed to expansions in Mexico, which feed into the U.S. market.
As for lumber production, several new mills and mill expansions are in the works in the South. Softwood lumber mill capacity in North America is approximately 74 billion board feet per year. Over the last decade or so, mills have moved from the West to the South, which is now the largest softwood lumber-producing region in North America. Last September, Forisk Consulting [https://forisk.com/] announced, “Based on announced sawmill builds and expansions, the U.S. South could add an additional four billion board feet of softwood sawmill capacity by 2022.” According to the announcement, the region’s plans for increased production included: “47 mill capacity increases, which includes 12 new mills and four reopenings. Of note, Roseburg Forest Products is building a 400 MMBF sawmill in Weldon, North Carolina. Recently, there have been several new announcements in Louisiana. These include the Canfor 250 MMBF greenfield sawmill in DeRidder, Interfor’s planned reopening of the former GP Dequincy 200 MMBF sawmill, and the partnership with Hunt and Tolko to build a 320 MMBF sawmill in Taylor, Louisiana.”
Look For Opportunities
Consumers are still looking for ADUs and home offices. According to a recent report from the NAHB, homeowners jumped on the opportunity to update their homes with home office spaces. With the onset of the pandemic, and the number of people working from home at an all-time high, homeowners realized they needed a dedicated home office space. That trend is expected to continue throughout 2022.
The NAHB also reported that interest in accessory dwelling units (ADUs) is growing. “Increased approval from planning and building departments has boosted ADU popularity,” the report says, “especially as a housing solution for homeowners needing space for returning grown children, for renters to help meet the shortage of affordable housing, and older parents wanting to age in place privately.”
There’s no doubt 2022 will continue to see its fair share of challenges. However, within those challenges are opportunities. Don’t be committed to doing what you’ve always done if it’s not working … especially when your biggest opportunities may be in new areas. GSCB